Porositeit, discontinuïteiten van het holtetype die worden gevormd door gasinsluiting tijdens het stollen, is een veel voorkomend maar lastig defect bij MIG-lassen en heeft verschillende oorzaken.Het kan verschijnen in semi-automatische of gerobotiseerde toepassingen en vereist in beide gevallen verwijdering en herbewerking, wat leidt tot uitvaltijd en hogere kosten.
De belangrijkste oorzaak van porositeit bij het lassen van staal is stikstof (N2), dat in het lasbad terechtkomt.Wanneer de vloeistofplas afkoelt, wordt de oplosbaarheid van N2 aanzienlijk verminderd en komt N2 uit het gesmolten staal en vormt het bellen (poriën).Bij gegalvaniseerd/galvanneal lassen kan verdampt zink in het lasbad worden geroerd en als er niet genoeg tijd is om te ontsnappen voordat het bad stolt, vormt het porositeit.Bij het lassen van aluminium wordt alle porositeit veroorzaakt door waterstof (H2), net zoals N2 in staal werkt.
Lasporositeit kan extern of intern verschijnen (vaak porositeit onder het oppervlak genoemd).Het kan zich ook ontwikkelen op een enkel punt op de las of over de gehele lengte, wat resulteert in zwakke lasnaden.
Als u weet hoe u enkele belangrijke oorzaken van porositeit kunt identificeren en hoe u deze snel kunt oplossen, kunt u de kwaliteit, productiviteit en bedrijfsresultaten verbeteren.
Slechte beschermgasdekking
Slechte beschermgasdekking is de meest voorkomende oorzaak van lasporositeit, omdat hierdoor atmosferische gassen (N2 en H2) het smeltbad kunnen verontreinigen.Gebrek aan goede dekking kan om verschillende redenen voorkomen, inclusief maar niet beperkt tot een slechte stroomsnelheid van het beschermgas, lekken in het gaskanaal of te veel luchtstroom in de lascel.Te hoge reissnelheden kunnen ook een boosdoener zijn.
Als een operator vermoedt dat een slechte stroming het probleem veroorzaakt, probeer dan de gasstroommeter af te stellen om er zeker van te zijn dat de snelheid voldoende is.Bij gebruik van een sproei-overdrachtsmodus zou bijvoorbeeld een stroom van 35 tot 50 kubieke voet per uur (cfh) voldoende moeten zijn.Lassen bij hogere stroomsterktes vereist een toename van het debiet, maar het is belangrijk om het debiet niet te hoog in te stellen.Dit kan leiden tot turbulentie in sommige pistoolontwerpen die de dekking van het beschermgas verstoren.
Het is belangrijk op te merken dat verschillend ontworpen pistolen verschillende gasstroomkarakteristieken hebben (zie twee voorbeelden hieronder).De 'sweet spot' van het gasdebiet is bij het topdesign een stuk groter dan bij het bottomdesign.Dit is iets waar een lasingenieur rekening mee moet houden bij het opzetten van de lascel.
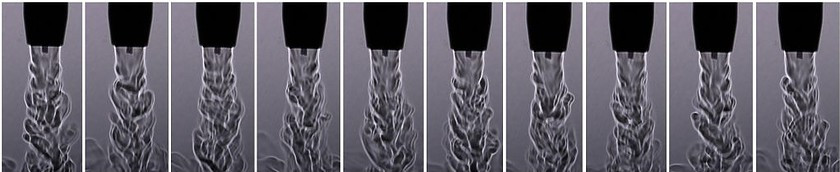
Ontwerp 1 toont een gelijkmatige gasstroom bij de mondstukuitlaat
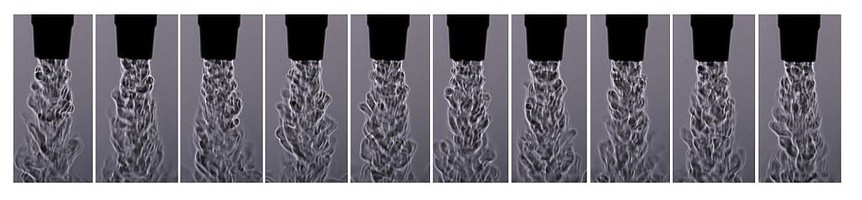
Ontwerp 2 toont een turbulente gasstroom bij de mondstukuitlaat.
Controleer ook op schade aan de gasslang, fittingen en connectoren, evenals O-ringen op de stroompen van het MIG-laspistool.Vervang indien nodig.
Wanneer u ventilatoren gebruikt om operators of onderdelen in een lascel af te koelen, zorg er dan voor dat ze niet direct op het lasgebied worden gericht waar ze de gasdekking kunnen verstoren.Plaats een scherm in de lascel ter bescherming tegen externe luchtstromen.
Raak het programma in robottoepassingen opnieuw aan om er zeker van te zijn dat er een juiste afstand tussen punt en werkstuk is, die doorgaans ½ tot 3/4 inch is, afhankelijk van de gewenste lengte van de boog.
Ten slotte, lage verplaatsingssnelheden als de porositeit aanhoudt of raadpleeg een leverancier van MIG-pistolen voor verschillende front-end componenten met een betere gasdekking.
Onedel metaalverontreiniging
Verontreiniging met basismetaal is een andere reden waarom porositeit optreedt - van olie en vet tot walshuid en roest.Vocht kan deze discontinuïteit ook bevorderen, vooral bij het lassen van aluminium.Dit soort verontreinigingen leidt doorgaans tot uitwendige porositeit die zichtbaar is voor de operator.Gegalvaniseerd staal is gevoeliger voor porositeit onder het oppervlak.
Om uitwendige porositeit tegen te gaan, moet u ervoor zorgen dat u het basismateriaal grondig reinigt voordat u gaat lassen en overweeg om lasdraad met een metalen kern te gebruiken.Dit type draad heeft hogere niveaus van deoxidatiemiddelen dan vaste draad, dus het is toleranter voor eventuele achtergebleven verontreinigingen op het basismateriaal.Bewaar deze en eventuele andere draden altijd in een droge, schone ruimte met een vergelijkbare of iets hogere temperatuur dan de plant.Door dit te doen, wordt condensatie geminimaliseerd die vocht in het lasbad zou kunnen brengen en porositeit zou kunnen veroorzaken.Bewaar draden niet in een koel magazijn of buiten.
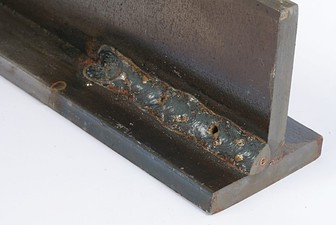
Porositeit, discontinuïteiten van het holtetype die worden gevormd door gasinsluiting tijdens het stollen, is een veel voorkomend maar lastig defect bij MIG-lassen en heeft verschillende oorzaken.
Bij het lassen van gegalvaniseerd staal verdampt het zink bij een lagere temperatuur dan het staal smelt, en hoge voortloopsnelheden hebben de neiging om het lasbad snel te laten bevriezen.Dit kan zinkdamp in het staal vasthouden, wat resulteert in porositeit.Bestrijd deze situatie door de rijsnelheden te monitoren.Overweeg opnieuw speciaal ontworpen (flux-formule) draad met metalen kern die de ontsnapping van zinkdamp uit het lasbad bevordert.
Verstopte en/of ondermaatse spuitmonden
Verstopte en/of te kleine spuitmondjes kunnen ook porositeit veroorzaken.Lasspatten kunnen zich ophopen in het mondstuk en op het oppervlak van de contacttip en diffusor, waardoor de beschermgasstroom wordt beperkt of turbulent wordt.Beide situaties verlaten het smeltbad met onvoldoende bescherming.
Deze situatie wordt nog verergerd door een mondstuk dat te klein is voor de toepassing en meer vatbaar is voor grotere en snellere opbouw van spatten.Kleinere mondstukken kunnen een betere toegang tot de gewrichten bieden, maar kunnen ook de gasstroom belemmeren vanwege de kleinere dwarsdoorsnede die is toegestaan voor de gasstroom.Houd altijd rekening met de variabele van de contacttip tot de uitsteek (of uitsparing) van het mondstuk, aangezien dit een andere factor kan zijn die de beschermgasstroom en porositeit beïnvloedt bij uw mondstukkeuze.
Zorg er daarom voor dat de spuitmond groot genoeg is voor de toepassing.Toepassingen met een hoge lasstroom waarbij grotere draadmaten worden gebruikt, vereisen doorgaans een mondstuk met grotere boringen.
Controleer bij semi-automatische lastoepassingen regelmatig op lasspatten in het mondstuk en verwijder deze met een lastang (welpers) of vervang het mondstuk indien nodig.Controleer tijdens deze inspectie of de contacttip in goede staat verkeert en of de gasverspreider duidelijke gasopeningen heeft.Operators kunnen ook anti-spatpasta gebruiken, maar ze moeten ervoor zorgen dat ze de spuitmond niet te ver of te lang in de pasta dopen, aangezien overmatige hoeveelheden van de pasta het beschermgas kunnen verontreinigen en de spuitmondisolatie kunnen beschadigen.
Investeer bij een gerobotiseerde lasoperatie in een mondstukreinigingsstation of ruimer om ophoping van spatten tegen te gaan.Dit randapparaat reinigt het mondstuk en de diffusor tijdens routinematige pauzes in de productie, zodat dit geen invloed heeft op de cyclustijd.Sproeierreinigingsstations zijn bedoeld om te werken in combinatie met een antispatsproeier, die een dunne laag van de verbinding op de frontcomponenten aanbrengt.Te veel of te weinig antispatvloeistof kan resulteren in extra porositeit.Het toevoegen van een luchtstroom aan een reinigingsproces voor spuitmonden kan ook helpen bij het verwijderen van losse spatten van de verbruiksartikelen.
Behoud van kwaliteit en productiviteit
Door het lasproces zorgvuldig te bewaken en de oorzaken van porositeit te kennen, is het relatief eenvoudig om oplossingen te implementeren.Als u dit wel doet, kunt u zorgen voor een langere inschakeltijd, kwaliteitsresultaten en meer goede onderdelen die door de productie gaan.
Posttijd: 02-02-2020